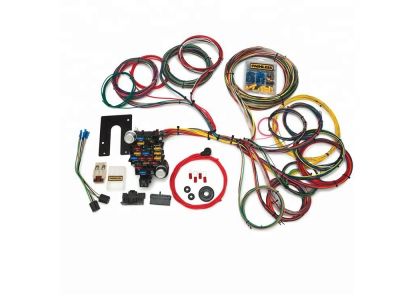
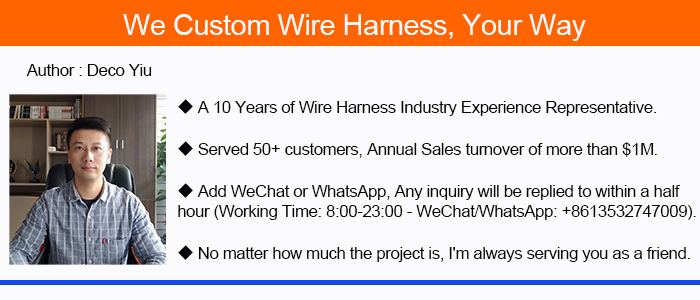
Introduction
Complex chassis wire harnesses are the lifeblood of modern electrical systems in various industries, including automotive, aerospace, and electronics. These intricate networks of wires and connectors play a crucial role in ensuring seamless electrical connectivity and functionality within a machine or vehicle. In this article, we will delve into the step-by-step process of creating a complex chassis wire harness, highlighting the essential stages involved in its design, assembly, and testing.
1.Designing the Blueprint
The foundation of any successful complex chassis wire harness project is meticulous planning and design. Before any physical work begins, engineers must create a detailed drawing that serves as a roadmap for the entire process. This drawing is not just a set of lines and shapes; it encapsulates the engineer's understanding of the project's intricacies.
To create an effective drawing, engineers need to comprehend the process details step by step. This understanding should encompass the precise specifications of each wire, connector, and component involved. The drawing should include information about wire gauges, lengths, connector types, and their respective locations within the harness.
Additionally, the draft drawing should serve as a guide during sample production. It should include annotations and notes that highlight critical points for the production team. These notes can be related to special handling requirements, materials to be used, or quality standards that must be met.
Furthermore, process instructions and Standard Operating Procedures (SOPs) are indispensable. SOPs provide a standardized framework that helps the production department understand what steps to follow and how to execute them correctly. These documents serve as a crucial bridge between design and production, ensuring that the final product aligns with the initial vision.
2.Wire Cutting and Crimping
Once the design is finalized, the next step is wire cutting and crimping. This phase involves precision and attention to detail. Technicians must adhere to the specifications outlined in the design, including wire lengths, gauges, and connector types.
Before handling any wires, technicians must ensure that the machinery is set up correctly. Proper calibration and adjustment of wire cutting and crimping machines are essential to guarantee that each wire and terminal meets the IPC/WHMA/A-620 standard. This standard defines the criteria for wire and terminal quality, including parameters such as pull force and electrical conductivity.
Testing the pull force of crimped terminals is a critical step in quality assurance. A crimp connection that doesn't meet the required pull force can result in unreliable electrical connections, which can have severe consequences in applications where safety and reliability are paramount.
3.Labeling for Clarity
After wires and terminals are cut and crimped, the next step is labeling. Labeling is a crucial aspect of Wire Harness Assembly, as it aids in identifying and tracing individual wires within the complex network.
Each wire should be labeled with a unique identifier that corresponds to the design drawing. These labels may include alphanumeric codes, color coding, or other visual markers that facilitate easy identification. Labeling ensures that wires are correctly routed and connected during the assembly phase and simplifies troubleshooting and maintenance in the future.
4.Precise Assembly
With all wires cut, crimped, and labeled, it's time to bring them together in precise assembly. Assemblers follow the design drawing meticulously, connecting wires and components according to the specified configuration.
The assembly process may involve securing wires to a board or chassis using clips, ties, or other fastening mechanisms. It's essential to ensure that the physical arrangement matches the drawing precisely to maintain electrical integrity and prevent interference or damage during use.
During assembly, technicians must pay close attention to detail, avoiding any potential issues such as crossed wires, loose connections, or improper routing. Errors in assembly can lead to malfunctions or electrical shorts, which can be time-consuming and costly to rectify.
5.Rigorous Testing
Once the complex chassis wire harness is assembled, it's time for rigorous testing. Testing is the stage where the electrical circuits are evaluated to ensure they function as intended.
Testing encompasses a range of procedures, including continuity checks, insulation resistance tests, and functional testing. Continuity checks verify that all intended electrical connections are intact, while insulation resistance tests ensure that there are no unintended electrical paths due to insulation faults.
Functional testing assesses the overall performance of the wire harness within the system it's intended for. This stage may involve simulating real-world operating conditions to validate that the harness functions reliably under various scenarios.
6.Packaging for Protection
After the wire harness has passed all testing and quality checks, it's ready for packaging. Proper packaging is essential to protect the harness during shipping and installation.
Packaging should take into account factors such as the harness's size, shape, and fragility. It should provide adequate cushioning and protection against moisture, dust, and physical damage. Additionally, labeling on the packaging should clearly indicate the contents and any handling instructions for safe transportation and installation.
Conclusion
The creation of complex chassis wire harnesses is a meticulous and highly specialized process that demands precision, attention to detail, and adherence to industry standards. From the initial design phase to assembly, testing, and packaging, each step plays a vital role in ensuring the reliability and functionality of the harness within its intended application.
Moreover, effective communication and collaboration between design engineers and production technicians are paramount to the success of such projects. Clear design documentation, process instructions, and quality standards serve as guiding lights throughout the journey from concept to a fully functional wire harness.
As industries continue to advance and demand ever more complex electrical systems, the expertise, and craftsmanship required for crafting complex chassis wire harnesses will remain a critical part of modern manufacturing. By following these steps and upholding rigorous quality standards, manufacturers can ensure that these essential components perform flawlessly in their intended applications.